Per molte aziende la “questione ambientale” non è più solo un impegno o un adempimento, ma sta diventando una nuova occasione per aumentare la competitività, per generare nuovo valore. Per questo i percorsi di innovazione sono sempre più orientati a cercare una nuova sintesi tra lo sviluppo del business e la responsabilità ambientale e sociale.
Ed è proprio in questa direzione che si colloca l’interessante esperienza di Cosberg, azienda specializzata nella progettazione e produzione di macchine customizzate che automatizzano processi di assemblaggio con un percorso che unisce i temi della servitization con quelli della valorizzazione di nuove opportunità in termini di riduzione dell’impatto ambientale così come emerge dalle analisi che ASAP Service Management Forum sta dedicando a questa relazione.
Alice Viscardi, Digital process specialist e Mauro Viscardi, special project innovation in Cosberg ci accompagnano nella conoscenza di un progetto che vede una importante evoluzione, sia in termini di modello di business, sia di raggiungimento di obiettivi di sostenibilità. Un progetto in cui si passa da una visione “prodotto centrica” a una che integra prodotti e servizi e che risponde, nello stesso tempo, alla domanda di maggiore flessibilità produttiva e di ottimizzazione sempre più precisa delle risorse energetiche e dei materiali.
Per i produttori di impianti questi obiettivi sono particolarmente importanti in un mercato che chiede di “fare di più con meno”. Come state rispondendo?
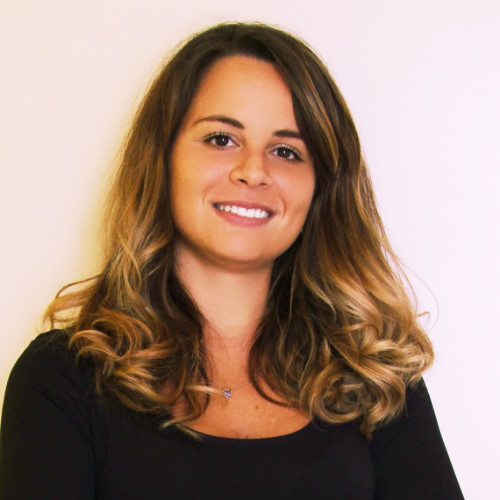
Uno dei punti qualificanti per i produttori di macchine sta proprio nella capacità di trasformare l’impianto in modo da farlo diventare un mezzo per erogare una capacità produttiva ed è in questo scenario che si colloca l’evoluzione dei sistemi e il rapporto con le imprese clienti.
Per comprendere la portata di questa evoluzione occorre partire dai bisogni dei clienti. I prodotti assemblati dalle nostre macchine hanno un ciclo di vita sempre più breve e per questo vediamo aumentare le richieste di flessibilità. La servitizzazione ci abilita prima di tutto a soddisfare al meglio queste richieste grazie al passaggio da un modello che prevedeva la vendita dell’impianto, a un modello che prevede la erogazione di capacità produttiva. In questo senso ci sono due grandi percorsi che stiamo affrontando in parallelo: uno è quello dei servizi e l’altro è quello degli impianti.
Partiamo dall’evoluzione dei servizi
In questo ambito abbiamo vissuto tre scenari. In una prima fase che ci ha accompagnato dagli anni ‘80 sino agli anni ‘2000 il prodotto era supportato da servizi di base, focalizzati attorno alla vendita come i ricambi, la manutenzione, il supporto. Il secondo scenario è quello attuale, con servizi intermedi focalizzati sulle condizioni del prodotto e sul mantenimento delle migliori condizioni produttive con un corredo di servizi di collaudo e assistenza da remoto, di monitoraggio, di manutenzione programmata e di training del personale. Il terzo scenario è abilitato dai servizi attuali e prevede che l’impianto non sia più venduto, ma che venga messa disposizione la sua capacità produttiva. L’impianto diventa di fatto il mezzo attraverso il quale questa capacità produttiva viene prodotta ed erogata.
Come vi state organizzando per quanto attiene all’evoluzione degli impianti?
In questo caso dobbiamo sottolineare che la sfida per le aziende che producono macchine per l’assemblaggio sta sempre più nella capacità di offrire maggiori opportunità in termini di personalizzazione dei prodotti finali, ovvero del prodotto che viene assemblato dalle nostre macchine impianti. Per perseguire al meglio questo obiettivo, stiamo ripensando tutta l’architettura dei nostri sistemi in modo tale da permettere una riconfigurazione efficiente dell’impianto in funzione delle esigenze di produzione. Per questo, abbiamo lavorato sulla struttura delle macchine, concepite come moduli standard dal punto di vista di hardware, software, monitoraggio e interfacce. Una scelta che permette una “riconfigurazione” in funzione delle necessità produttive. Questo modello abilita il passaggio a una logica di noleggio dell’impianto in funzione delle missioni produttive che è chiamato a svolgere.
Un cambiamento quindi a livello di ingegnerizzazione delle macchine per abilitare un cambiamento anche a livello di modello di business?
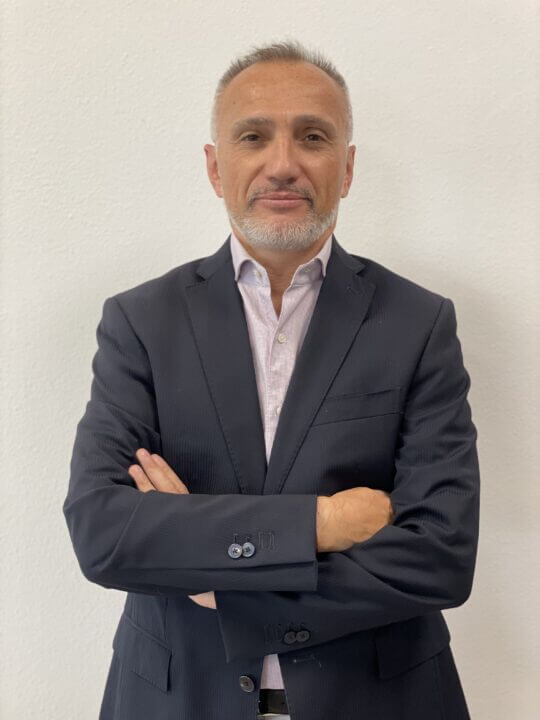
Sì, ed è qui si aggiunge anche il tema della sostenibilità. L’impianto è ingegnerizzato a moduli che permettono una personalizzazione della capacità produttiva in funzione del concetto di missione produttiva, ovvero degli obiettivi del cliente. I moduli a loro volta sono progettati per essere rigenerabili e riutilizzabili per altre missioni produttive.
Come state procedendo?
Stiamo introducendo una serie di strumenti digitali che abilitano questo nuovo percorso in termini di gestione della capacità produttiva da remoto, ma anche di gestione del ciclo di vita della macchina, che può essere “allungato” – oggi attraverso un revamping rapido – e che si può concretizzare in futuro presso diversi clienti per soddisfare diverse missioni produttive.
Con il percorso di servitizzazione ci stiamo attrezzando per progettare un riutilizzo dell’impianto anche al momento del suo rientro una volta terminata la sua missione produttiva presso un cliente. L’impianto torna così in Cosberg, viene inserito in processi di de-manufacturing e re-manufacturing e i moduli possono essere rigenerati e riutilizzati per dare vita ad un nuovo impianto configurato per altre missioni produttive. La macchina, del resto, è da sempre progettata in modo modulare, come una sorta di sistema costruito con la logica dei “mattoncini Lego”.
In particolare, per attuare questo percorso abbiamo cercato di rappresentare in digitale la nostra azienda, abbiamo identificato quelli che sono gli strumenti chiave che abiliteranno questa nuova visione a partire dal PLM, uno strumento fondamentale che ci permetterà di gestire tutto il ciclo di vita delle macchine.
Servitizzazione come fattore abilitante per un avvicinamento a logiche di economia circolare?
Con questa strategia, possiamo concretamente passare da un’economia lineare in cui con il commissioning si cede l’impianto e con esso la responsabilità sul suo impatto ambientale, a una logica vicina all’economia circolare in cui noi come Cosberg ci assumiamo la responsabilità di tutto il ciclo di vita della macchina, anche per quanto attiene alla fase di riciclo e di recupero quando l’impianto ha terminato la sua missione produttiva.
Una trasformazione anche nella missione aziendale?
Certamente, con questo modello di business non solo aggiungiamo servizi alla nostra offerta commerciale, ma diventiamo dei Service provider e confermiamo e rafforziamo l’obiettivo di migliorare i processi produttivi del nostro cliente, rendendolo concretamente più competitivo.
Possiamo definirlo come un percorso di sostenibilità by design?
Diciamo subito che il modello di business Cosberg è fortemente basato sulla centralità della persona e sulle competenze. Ci siamo posti l’obiettivo di realizzare impianti produttivi sostenibili partendo dal presupposto di creare macchine che permettano alle aziende clienti di raggiungere i loro obiettivi di sostenibilità. E lo abbiamo fatto introducendo tecnologie in grado di ripensare in chiave di sostenibilità l’intero impianto produttivo dalla gestione dell’energia alla gestione dei materiali.
In questo senso con sostenibilità by design, intendiamo l’uso di tecnologie che ci consentono di rendere sempre più riconfigurabili i nostri impianti, cercando un compromesso tra la richiesta del mercato che necessita di cambiare più velocemente la propria capacità produttiva e la necessità di allungare la durata del ciclo di vita degli impianti, a cui si aggiunge anche una ottimizzazione nella gestione dei materiali necessari per la produzione stessa.
Prosegui la lettura delle strategie e delle esperienze di sustainability manager di importanti aziende e organizzazioni.
Immagine fornita da Shutterstock