Le priorità dettate dalla domanda di sostenibilità stanno cambiando profondamente tanti mercati e il mondo manifatturiero, assai più di altri settori, è chiamato a contribuire a questa trasformazione. La sustainability transformation è strettamente connessa e abilitata dalla digital transformation e per le imprese del manufacturing, si traduce in una trasformazione industriale che agisce sui prodotti, sui processi, sul rapporto con i clienti e sui modelli di business.
Le spinte in questa direzione sono tante e sempre più forti: ci sono le esigenze dei consumatori, che chiedono prodotti sostenibili e che esigono informazioni e dati sulla sostenibilità e ci sono, grazie anche all’ESG, le istanze del mondo della finanza che stanno spingendo verso una trasformazione basata sull’innovazione digitale come fattore abilitante.
Nello stesso tempo, le aziende sono sempre più ricche di dati e si presenta in maniera urgente la necessità di valorizzare in modo innovativo questi dati. Se si guarda alle fonti di un Internet of Things sempre più presente negli stabilimenti o nelle infrastrutture e dell’Industrial IoT – a sua volta corredo indispensabile di prodotti e sistemi di produzione – si dispone di una “ricchezza” che cresce ogni giorno ma che ha bisogno di essere trasformata in conoscenza.
E appare oggi sempre più chiaro che si tratta di un processo che porta valore anche attraverso la identificazione e la creazione di una serie di nuovi vantaggi, che vanno dall’ottimizzazione dei consumi alla gestione delle risorse, dalla sicurezza alla riduzione dei rischi, dalla creazione di nuove forme di relazione tra produttori e clienti all’attivazione di nuovi modelli di business. In questo contesto, si collocano anche le logiche e le prospettive dell’economia circolare e della manifattura circolare che contribuiscono a cambiare le catene del valore del manifatturiero.
Questi temi e il ruolo del digitale come vettore di trasformazione industriale, di raggiungimento di obiettivi di sostenibilità e di ESG e come piattaforma di competitività sono stati al centro dell’approfondimento speciale “Le opportunità per le aziende manifatturiere tra AI, ESG ed economia circolare” che si è tenuto in occasione dell’edizione 2022 dell’evento Industry 4.0 360 Summit organizzato dalle testate InnovationPost, Industry4Business e ESG360 del Gruppo Digital360. La sessione dedicata a questo tema ha visto la partecipazione di:
- Nicola Saccani, Professore Associato, Laboratorio RISE dell’Università degli Studi di Brescia
- Antonio Gentile, EMEA Data Centric Workload SAP Specialist Presales, Dell Technologies
- Walter Riviera, AI Technical Lead EMEA, Intel
- Claudia Angelelli, Senior Manager Solution Engineering, VMware
Manifatturiero, sostenibilità, ESG ed economia circolare
“Sappiamo che c’è una spinta forte verso una maggiore sostenibilità dei processi del manifatturiero e una grande riflessione è in corso sui temi del ciclo di vita dei prodotti – osserva Nicola Saccani, Professore Associato, Laboratorio RISE dell’Università degli Studi di Brescia -. Una spinta che arriva da tanti fenomeni come il cambiamento climatico, l’inquinamento, le criticità legate alla produzione e alla gestione di rifiuti, ma anche la scarsità di materie prime, (fenomeno sempre più rilevante soprattutto in questo periodo al pari della disponibilità di componenti semi-lavorati) e le complessità legate alla crisi nelle catene di fornitura e alla volatilità dei prezzi”. Tutti fattori che generano congiuntamente una crescente instabilità del business e delle attività industriali in generale.
In questo contesto, l’adozione di un “approccio di economia circolare permette di mitigare i rischi e di generare una crescita sostenibile per le aziende, sia dal punto di vista ambientale che economico. Infatti, – prosegue Saccani – l’economia circolare grazie alla capacità di disaccoppiare la crescita economica dal consumo di risorse, consente anche di ridurre ed eliminare il concetto stesso di rifiuto”.
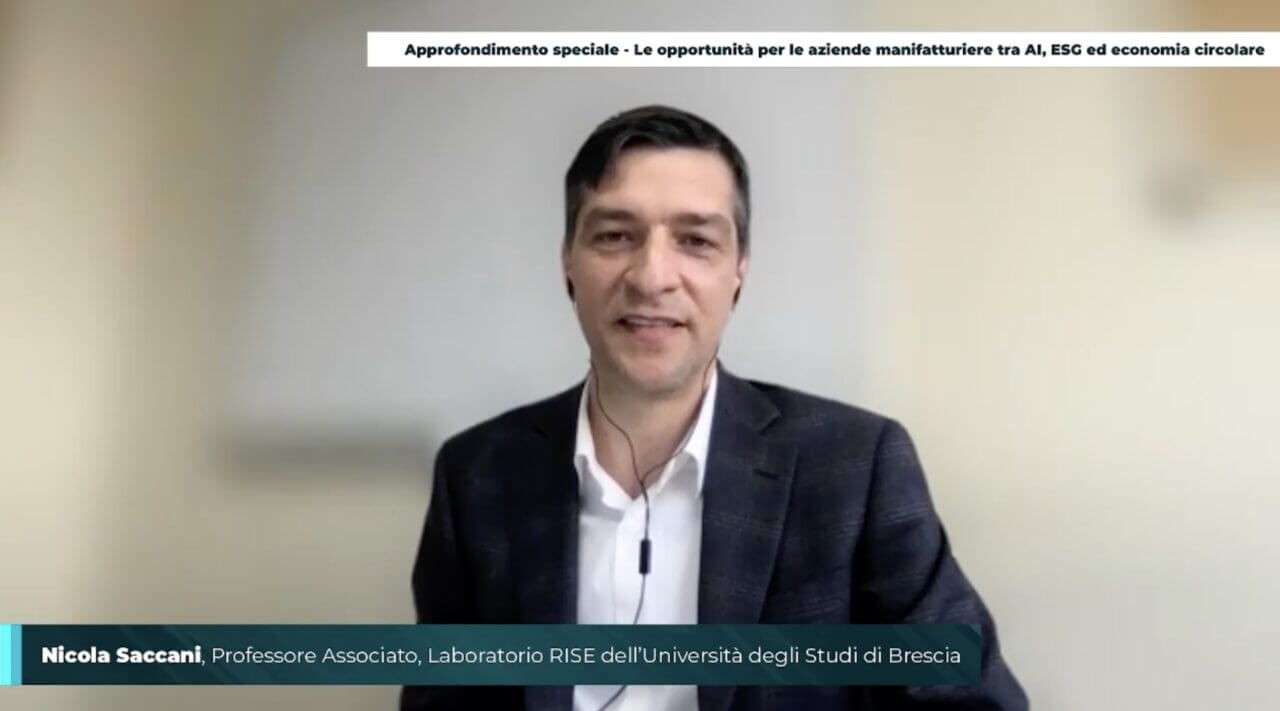
Il paradigma delle quattro “R”
In questo senso, Saccani richiama il paradigma delle quattro R (Reduce, Reuse, Recover, Recycling) in un approccio alla produzione che “impone” di ridurre il consumo delle risorse con una serie di modalità che prevedono tra i vari temi l’estensione della vita utile dei prodotti; la capacità di riutilizzare un bene rimettendolo in circolo quando arriva alla fine del ciclo di vita; la possibilità di ricondizionare (e di attuare forme di remanufacturing) scomponendo il bene e utilizzandone le singole parti; e come “ultima spiaggia”, la necessità di riciclare i materiali che compongono il bene.
Tutto questo si raggiunge tramite un processo di trasformazione disruptive che si basa su una serie di attività che impongono un ripensamento dei processi basati sui dati. “Si parte dal processo produttivo con innovazioni incrementali o radicali che aiutano a ridurre il consumo delle risorse, a eliminare o riutilizzare gli scarti, a utilizzare materie prime seconde anziché materie prime vergini, a disegnare un processo di lavorazione basato su materiali sostenibili e riciclabili, piuttosto che adottare pratiche di sviluppo dei prodotti che puntino sulla modularità, sulla possibilità di “disassemblare” più facilmente i prodotti, ma anche su logiche di manutenzione rafforzate per consentire il raggiungimento della circolarità. In questo senso Saccani ribadisce la necessità di lavorare sulle supply chain anche in logica di reverse logistics, per organizzare processi che permettano di riprendere il controllo di materiali e prodotti a fine vita, di organizzare il loro recupero dagli utilizzatori finali con il coinvolgimento in diverse forme dei partner della supply chain.
Digitalizzazione come fattore abilitante per la sostenibilità
In tutto questo, la digitalizzazione è un fattore abilitante importantissimo: grazie a fattori come la dematerializzazione, la simulazione, i data analytics e tante altre si possono svolgere le stesse attività del “mondo fisico” con migliori risultati e riducendo l’impatto ambientale.
Lo smart working sul piano del lavoro ha mostrato quanti e quali risultati si possono conseguire, la prototipazione virtuale e i digital twin consentono di ridurre drasticamente l’impatto ambientale, la stampa 3D a sua volta consente la produzione on site e on demand riducendo sprechi, costi e tempi, e annullando in larga misura anche l’impatto legato ai trasporti, rispetto alle modalità di produzione di tipo sottrattivo.
Lo scenario delle possibilità legate alle tecnologie abilita la progettazione di un futuro più sostenibile e tutto questo può a sua volta tenere conto del fenomeno della digital servitization che passando da logiche di vendita dei beni dal fornitore al cliente, a logiche di noleggio, pay-per-use e servitizzazione permette di mantenere un maggior controllo e incentiva comportamenti virtuosi nel ciclo di vita di beni e servizi.
“La tecnologia è certamente un fattore abilitante – conclude Saccani -, ma non è una condizione sufficiente. Occorre accompagnare questo lavoro con un forte impegno sulle strategie, sulle competenze, sulla motivazione nella determinazione a un uso attento delle tecnologie perché anche queste hanno un impatto ambientale. Occorre poi imparare a integrare più informazioni di supporto alle decisioni basate su tematiche ambientali rispetto a quelle che oggi si trovano normalmente nei sistemi informativi aziendali che puntano tipicamente al costo, alla quantità, all’efficienza mentre è sempre più importante tracciare e valorizzare elementi collegati ai temi della sostenibilità”.
Gentile, Dell Technologies: dalla disponibilità del dato alla sua trasformazione in valore
Per le aziende manifatturiere italiane la trasformazione industriale, dettata anche dai temi della sostenibilità, è legata alla capacità di far valere i dati di cui dispongono, di mettere a valore il grande potenziale, ad esempio ma non solo, dell’Industrial Internet of Things. Per questo servono tecnologie e modelli unitamente alla capacità di sperimentare e di avviare percorsi di innovazione.
Antonio Gentile, EMEA Data Centric Workload SAP Specialist Presales, Dell Technologies sottolinea che occorre guardare prima di tutto a un percorso che parte dalla disponibilità del dato e che arriva alla sua trasformazione in valore. “Oggi le aziende del manifatturiero con impianti di produzione, dispongono di macchinari che producono grandi quantità di dati, il punto è che non essendo connesse non li condividono. Per questo motivo, il primo passaggio da fare consiste nella connessione dei sistemi con un approccio che tenga conto da subito della necessità di garantire la sicurezza, perché una sistema di produzione collegato in modalità online risulta potenzialmente anche vulnerabile. Questo è il primo passo da fare in qualsiasi percorso di innovazione, saper garantire la sicurezza”.
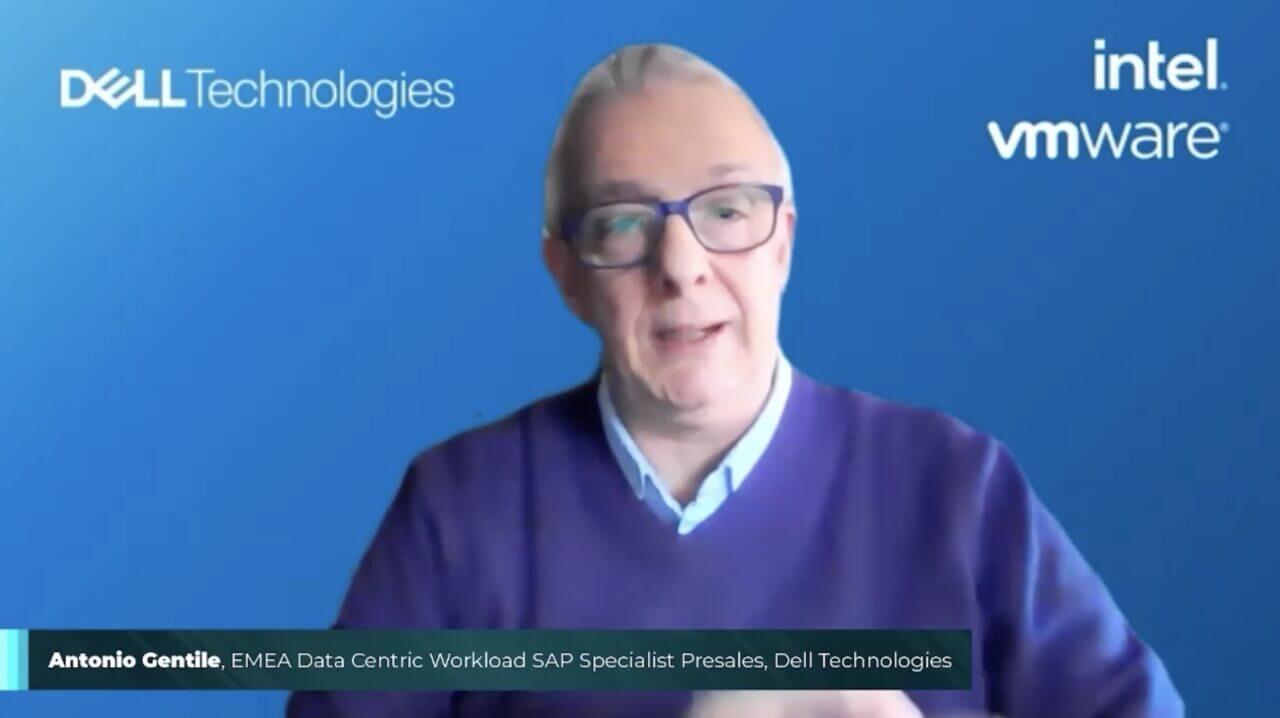
Per questo Gentile fa riferimento alla scelta di Dell Technologies di mettere a disposizione delle imprese del mondo della produzione prima di tutto una infrastruttura di Edge Computing a più livelli. “Una serie di soluzioni – spiega – in grado di portare nelle aziende in generale e nel manifatturiero in particolare, dove serve anche una capacità di elaborazione in real time, una intelligenza sicura con un primissimo livello che garantisca sia la data collection sia la protezione dei dati e dei sistemi”.
I dati poi sono tanti ed è sempre più importante che siano opportunamente selezionati per garantire il corretto “trattamento” in funzione degli obiettivi. Per questo è importante guardare al percorso che li porta a un “nodo” governato dall’Intelligenza Artificiale “questo aiuta ad effettuare una prima importante valutazione , ma soprattutto una selezione – spiega Gentile – tra il “dato veloce” e il “dato lento”.
Nello specifico, il dato veloce è legato a fattori che attengono direttamente e immediatamente a problematiche di business come possono essere quelle della manutenzione predittiva o di interventi diretti sui fattori di produzione in real time. Il “dato lento” è invece consegnato ad applicazioni che estraggono un valore che non deve incidere nell’immediato, che cioè non implica un intervento in tempo reale sulla produzione, ma che va ad alimentare processi decisionali basati su una conoscenza più estesa e completa”.
Nell’ambito del primo livello di “azione” entrano in gioco soluzioni basate su una grande potenza di elaborazione, grazie ad algoritmi di Intelligenza Artificiale che analizzano i dati fornendo un output finale che offre una rappresentazione precisa degli asset di produzione, anche in funzione del processo decisionale specifico di ciascuna azienda. “Nel caso dei produttori di macchine destinate alla produzione, ad esempio – spiega Gentile – questo significa che il produttore del macchinario è nella condizione di monitorare il sistema con la massima precisione, di effettuare manutenzione da remoto, di verificare come viene utilizzata e come deve essere personalizzata in funzione degli obiettivi del cliente. Può poi disporre di conoscenza da applicare alle logiche di supply chain per trasferire informazioni importanti e indicazioni all’impresa utente del macchinario per migliorare le performance di produzione e la gestione delle risorse”.
Una semplificazione del percorso di valorizzazione dei dati
Gentile tiene a sottolineare l’importanza di aver semplificato il processo di valorizzazione dei dati garantendo in modo completo e per tutto il processo il tema della sicurezza. “Partiamo dalla sensoristica che genera dati, proteggiamo la macchina – ripete – e proteggiamo i dati per garantire un output di gestione che sia effettivamente completo sia dal punto di vista del produttore dei sistemi sia per quanto attiene la gestione dei dati verso i clienti finali”.
Per ottenere questo risultato, Gentile ricorda che nel processo di valorizzazione del dato occorre fornire prospettive e competenze anche molto diverse e “per raggiungere questo obiettivo – spiega – Dell Technologies ha creato un Laboratorio chiamato Data Experience con una serie di player di riferimento come Intel, VMware, Suse, PTC. Una federazione complessa che conta sul supporto di un system integrator come Applied. In questo laboratorio reale i clienti possono portare i loro dati, possono affrontare i loro obiettivi di competitività e sostenibilità e le loro criticità con un servizio in grado di accompagnarli in un percorso che è sia di digital transformation sia di industrial transformation basato su un vero e importante gioco di squadra”.
Il ruolo dei Proof of Concept
“In otto mesi – prosegue Gentile – il Lab ha sostenuto la realizzazione di diversi Proof of Concept, PoC e un esempio importante in questo senso è rappresentato da IMA, azienda leader mondiale nel settore della produzione di macchine per il packaging negli ambiti del food and beverage, del pharma”. La possibilità di lavorare su dati reali ha permesso al PoC avviato nel Lab di innalzare di diversi punti percentuali l’affidabilità delle macchine e di trovare nuove forme di valore. In altri casi, come nell’esperienza avviata con un’azienda specializzata nella produzione di compressori, grazie all’analisi dei dati IoT legati alla produzione di aria compressa e grazie all’analisi dell’utilizzo finale da parte delle imprese utenti e delle prospettive di mercato, è stato possibile individuare un percorso di sviluppo per l’azienda che la porta a privilegiare la “vendita di aria compressa” rispetto alla vendita di sistemi di compressione.
Un percorso verso il Manufacturing as a Service
“In sostanza – prosegue Gentile – grazie al nostro laboratorio abbiamo potuto constatare che le aziende possono vedere questi dati da prospettive un tempo impraticabili e da queste “viste” nascono stream di business anche inaspettati che nel laboratorio si possono sperimentare e testare”. Siamo in un ambito che Gentile definisce come “manufacturing as a service” e siamo in una fase in cui le aziende possono mettere in discussione modelli di business consolidati, basati sulla vendita della macchina, per attuare nuove forme di valorizzazione. Il monitoraggio continuo permette poi di utilizzare logiche di pay per use in base alle dinamiche del mercato e di alzare il livello di personalizzazione sulle più specifiche esigenze dei clienti”.
Riviera, Intel: tutto parte dai dati, ma li si deve interrogare nel modo giusto
La risposta alla domanda di sostenibilità nelle imprese manifatturiere arriva anche da prodotti più intelligenti realizzati da sistemi di produzione e processi che diventano, a loro volta, più intelligenti. La sostenibilità a sé stante rischia di non essere un vero valore se non è in grado di diventare un asset di competitività. E questo processo è possibile solo grazie ai dati e grazie alla capacità di trasformarli in informazioni, in conoscenza e in decisioni. In questo processo, anche nel mondo manifatturiero un ruolo importante è svolto dall’Intelligenza Artificiale.
Per Walter Riviera, AI Technical Lead EMEA, Intel il punto chiave riguarda la necessità di rappresentare in formato digitale l’entità dei problemi che vogliamo indirizzare unitamente alla sfida di capire, all’interno dei dati che si hanno a disposizione, cosa è rilevante e cosa non lo è. “In funzione del task che ci poniamo – osserva – alcuni dati possono essere rilevanti altri lo sono meno e a seconda di come cambiamo gli obiettivi ci sono dati che da marginali o poco rilevanti diventano fondamentali se interpretati con una prospettiva diversa”.
È importante, come osserva Riviera: fare le domande giuste ai dati. Una professionalità che Riviera richiama con una metafora: “è un po’ come se a un imprenditore venisse data la possibilità di accedere a una stanza nella quale incontrare i più grandi guru dell’innovazione al mondo e intraprendere con loro un dialogo nel modo che ritiene più opportuno. Solo con le domande giuste potrà avere risposte che effettivamente potranno rivelarsi utili e aprirsi nuovi orizzonti. Si potrebbero paragonare le grandi collezioni di dati a grandi asset di conoscenza: il rischio è di esprimere poco valore se non li si interroga nel modo giusto”.
Favorire un cambio culturale per arrivare a una mentalità data driven
“Nella mia esperienza nell’ambito di progetti di intelligenza artificiale – spiega Riviera – ho avuto modo di confrontarmi con tante realtà e con tanti clienti in contesti in cui, per ottenere e sviluppare concretamente i vantaggi dell’Intelligenza Artificiale, è stato necessario stimolare e favorire un cambio culturale che va ben oltre l’utilizzo di tool e di tecnologie. É una questione di mentalità che deve orientarsi ai dati, deve ispirarsi a un metodo in cui le decisioni sono basate sull’analisi dei dati e su misurazioni oggettive”.
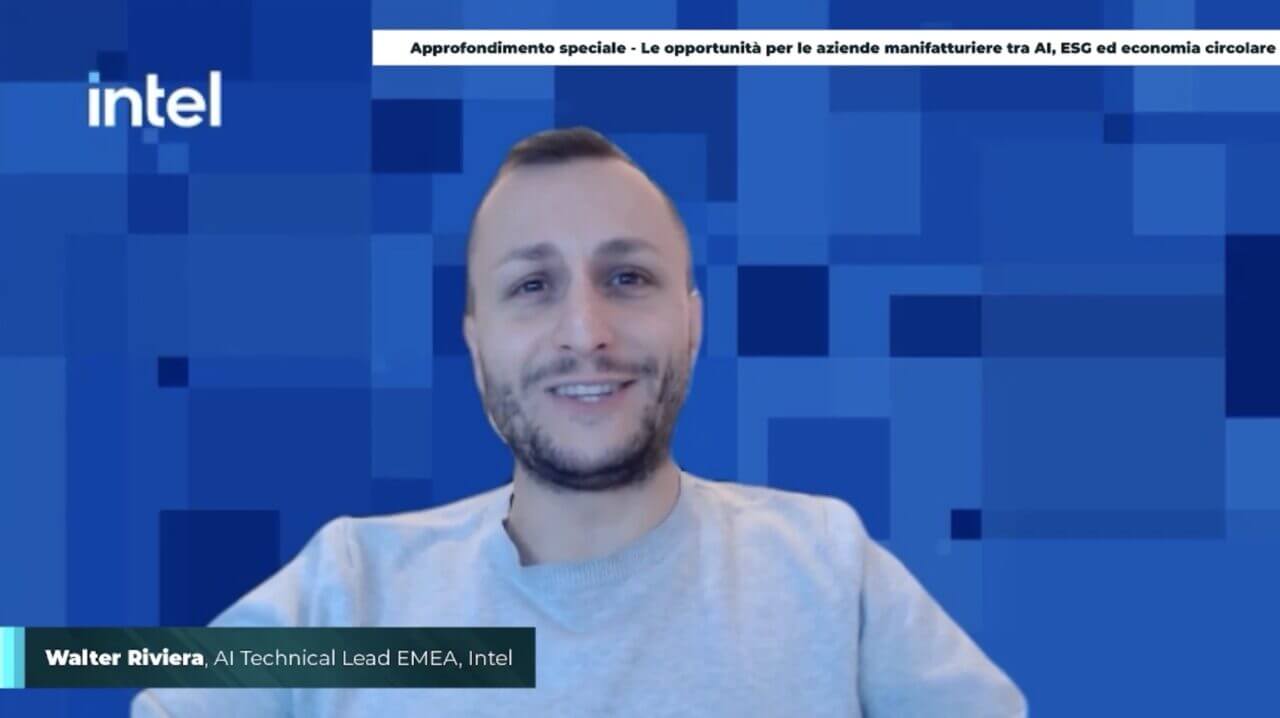
Il punto chiave attiene al “come” arrivare a creare queste condizioni e per Riviera l’indicazione riguarda la necessità di partire dall’analisi delle sfide e delle risorse. “Si procede – spiega – con la creazione di due grandi liste. Nella prima vengono elencate tutte le sfide che si possono attuare all’interno di un’azienda in termini di sviluppo prodotti, di attività commerciali, di tempi di produzione, di costi, di consumi energetici, di evoluzione nelle relazioni con i clienti. Ovvero tutte le sfide concrete che attengono alla creazione di valore delle imprese. A questa si aggiunge una seconda lista – prosegue – con tutti i dati a disposizione dell’azienda per indirizzare queste stesse sfide, un elenco il più possibile completo delle fonti di dati che l’azienda conosce e che può mettere a disposizione. Il terzo passaggio di questo metodo – conclude – attiene alla connessione delle due liste, alla individuazione del dato “giusto” per la sfida “giusta” e quindi alla identificazione dei dati e delle fonti che sono utili per migliorare ciascun specifico problema. La sintesi finale rappresenta un ottimo punto di partenza per la definizione delle priorità e delle azioni da effettuare”.
Sostenibilità: il primo step è la misurabilità
Per quanto attiene agli obiettivi legati alla sostenibilità, per Riviera occorre un’attenzione speciale e per questo è importante fare riferimento sempre e comunque ai temi della misurabilità. “Tutto deve partire dalla capacità di misurare e dalle osservazioni costanti dei fenomeni che incidono direttamente e indirettamente sulla sostenibilità. Questa osservazione è fondamentale anche per la definizione stessa degli obiettivi che si possono raggiungere. Occorre avere ad esempio – sottolinea – una panoramica chiara dei consumi attuali, da mettere in relazione con la produzione per definire concretamente come ridurre l’impatto ambientale aumentando il valore, occorre conoscere con precisione la quantità di scarti e come questi sono prodotti, per determinare sempre con precisione come e dove si possono evitare sprechi”.
“Siamo in un ambito basato sulla rappresentazione digitale della produzione che a sua volta si appoggia su una rappresentazione digitale della realtà e, grazie a questo modello, si possono applicare regole che consentono di individuare, grazie all’Intelligenza Artificiale, in quali punti si annidano eventuali errori e quali sono le aree di miglioramento sulle quali agire”.
Dai nuovi dati nascono nuove idee
Ma l’intelligenza artificiale deve procedere di pari passo con l’intelligenza e la sensibilità delle persone che la governano, prima di tutto perché la tecnologia dell’oggi è nata ieri ed è accompagnata e sostenuta dalle esperienze che si realizzano e dalle valutazioni con cui si guarda a queste esperienze e ai risultati ottenuti. Per poter disporre di una visione delle prospettive che si aprono per ciascuna azienda, Riviera suggerisce di guardare a tre fattori: il primo attiene alle risorse computazionali, il secondo alla quantità di dati a disposizione e il terzo riguarda le tecniche e le teorie attraverso le quali trasformare i dati in conoscenza e in valore.
“Si tratta di tre ingredienti che abbiamo a disposizione e che permettono di inventare costantemente nuove soluzioni. E quando si tratta di pensare ai casi di successo – osserva Riviera – mi piace pensare che i casi più belli probabilmente li dobbiamo ancora inventare perché abbiamo veramente tante potenzialità, e arrivano costantemente tanti nuovi dati che alimentano altrettante nuove idee”.
Migliorare la qualità come presupposto per raggiungere obiettivi di sostenibilità
Relativamente alle esperienze concrete che possono mostrare i vantaggi di un manifatturiero sempre più orientato ai dati Riviera richiama la collaborazione con John Deere, l’impresa statunitense produttrice di trattori, mezzi pesanti e attrezzature per il mondo dell’agricoltura. “Si tratta in questo caso di una Intelligenza Artificiale al servizio della qualità di produzione in diversi momenti tra cui il controllo delle saldature. Si tratta di una fase della produzione molto importante per questa azienda e in generale per il manifatturiero.
“Sostenibilità – afferma Riviera – non vuol dire solo fare di più con meno – precisa – ma vuole dire fare sempre meglio; difatti più aumenta la sostenibilità e meno materiali vengono sprecati, più aumenta la qualità, la sicurezza, la durata e l’affidabilità dei veicoli”. In questo caso l’intelligenza artificiale porta una capacità di controllo, di verifica, individuazione degli errori e di controllo di qualità che ha un impatto enorme e che si estende al controllo dell’accuratezza delle modalità di assemblaggio dei componenti.
Un altro esempio riguarda l’utilizzo dell’Intelligenza Artificiale per la sicurezza e la protezione dei lavoratori con un’applicazione che permette di verificare se gli addetti all’interno dei cantieri indossano effettivamente e correttamente i sistemi di protezione. È anche questa sostenibilità: una forma importante di sostenibilità che attiene alla dimensione personale in relazione al benessere e alla sicurezza dell’ambiente in cui le persone sono chiamate a operare e che ha come obiettivo di assicurare una maggiore qualità del lavoro.
Angelelli, VMware: la virtualizzazione al servizio di una sostenibilità intrinseca
La sostenibilità è una sfida quotidiana che grazie al digitale si collega in modo sempre più stretto alle sfide della competitività, della sicurezza e del raggiungimento di obiettivi ESG. Proprio in questo senso, VMware ha recentemente pubblicato il proprio report ESG dal quale emerge una relazione molto forte tra i temi dell’innovazione digitale e i temi della sostenibilità.
“A nostro avviso – osserva Claudia Angelelli, Senior Manager Solution Engineering, VMware – si tratta di un rapporto che permette di dare vita a logiche che chiamiamo di sostenibilità intrinseca, vale a dire una sostenibilità che si può realizzare per tutti i prodotti in modo nativo, con modalità legate direttamente al ripensamento dei prodotti stessi e dei processi di produzione”.
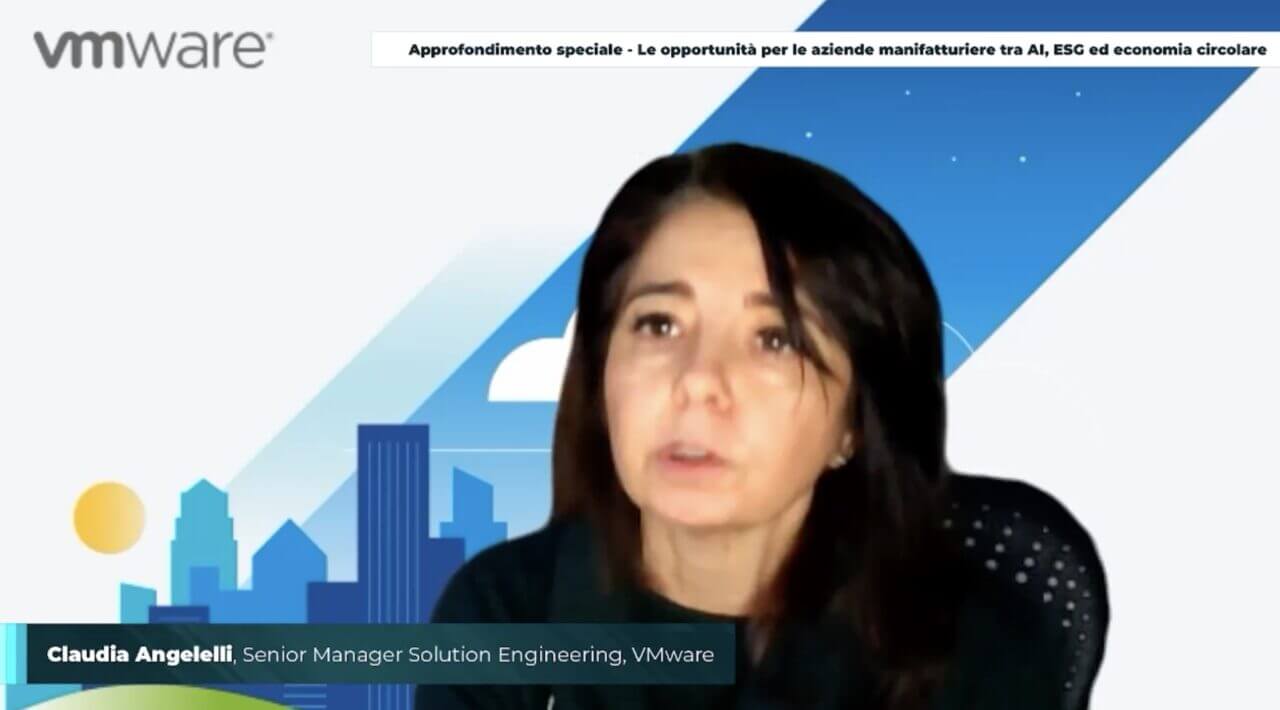
In particolare, il report parla di progetti attraverso i quali sono fissati gli obiettivi di sostenibilità dell’azienda “abbiamo individuato 30 progetti obiettivo da realizzare entro il 2030 – spiega – che puntano ai temi della sustainability, dell’equity e del trust e dal quale prende forma la capacità di mettere a disposizione dei clienti un supporto concreto per raggiungere i loro obiettivi di sostenibilità e di competitività grazie all’utilizzo di un’infrastruttura virtualizzata”.
La virtualizzazione al servizio dei dati nelle catene del valore
Soluzioni che grazie alla virtualizzazione permettono di raggiungere una sostenibilità a livello di ecosistema e di una gestione sempre più attenta alle risorse delle catene del valore. “Ad esempio – spiega – con l’ottimizzazione degli spazi, con la gestione delle risorse computazionali, con il controllo dei consumi. In concreto con la possibilità di andare nella direzione di smart cloud basata sull’utilizzo di qualsiasi tipo di Cloud grazie a una infrastruttura che consenta di gestire sia le applicazioni sia i dati”.
Il tutto perché il mondo manifatturiero ha bisogno di flessibilità, di disporre di soluzioni che consentano l’utilizzo dei dati a prescindere dal “luogo” in cui risiedono, rispondendo a questa domanda indipendentemente dal fatto che si debba fare riferimento a un data center aziendale o a qualsiasi tipo di cloud. “I dati – osserva – devono poter entrare rapidamente nella catena del valore delle imprese, devono poter essere utilizzati in funzione del loro potenziale, che si tratti di “dati” veloci” o di “dati lenti” devono poter contare su un controllo a 360° e le aziende devono poi essere anche nella condizione di misurare le loro azioni, devono disporre di strumenti che permettano di dare evidenza al cliente dei consumi e dei costi”.
La sostenibilità intrinseca deve essere prima di tutto una sostenibilità sicura
Il tutto per Angelelli deve poi essere assicurato con la massima attenzione alla sicurezza da considerare come un tema caldissimo e come un tassello fondamentale, perché negli impianti di produzione si lavora con dati che devono essere tutelati e protetti in tutte le condizioni e per i quali è necessario disporre di meccanismi di sicurezza che partano dal paradigma dello Zero Trust e che siano in grado di analizzare continuamente tutto ciò che accade su tutta la catena delle applicazioni.
In questo ambito Angelelli sottolinea il supporto dell’Intelligenza Artificiale che consente di attuare un’analisi puntuale permettendo di analizzare tutto ciò che accade con la massima precisione anche in relazione ai comportamenti degli utenti. E tornando al tema della sostenibilità intrinseca Angelelli enfatizza il fatto che si traduce anche nella capacità di garantire sicurezza e protezione dei dati in un contesto che permetta alle imprese del manifatturiero di utilizzarli con la massima flessibilità.
Tra le imprese del mondo manifatturiero impegnate in questo tipo di percorsi Angelelli cita il caso di Mercedes Benz in particolare per quanto attiene al servizio di configurazione delle vetture che permette ai clienti finali di disporre di un configuratore per scegliere e impostare la propria auto attraverso un meccanismo di micro-servizi basati sul cloud. Una soluzione che permette alla compagnia automobilistica tedesca di mettere a disposizione dei clienti una soluzione in grado di rispondere velocemente e in modo preciso alla domanda dell’utente finale, nonché di disporre di dati che rappresentano una conoscenza dettagliata delle esigenze. Un altro caso in cui la virtualizzazione ha permesso di creare nuovo valore è rappresentato da Michelin, che ha avuto la necessità di mettere in sicurezza l’utilizzo delle applicazioni operative in oltre 200 siti operativi nel mondo.