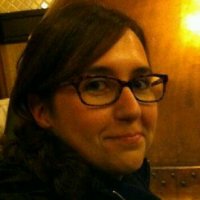
Salute e sicurezza nei luoghi di lavoro sono imperativi aziendali, non solo perché garantiscono l’incolumità dei lavoratori, ma anche perché aumentano la produttività e la qualità del prodotto. Non tutti, però, considerano che investire sulla salute può essere un fattore determinante, un vero driver per la crescita aziendale. Se è vero che i miglioramenti in termini di salute e sicurezza sono in grado di influenzare la produttività, è anche vero che devono essere accompagnati da un cambiamento “culturale” ed “organizzativo” che mira all’eccellenza, costruito su una visione aziendale condivisa, e ciò richiede un impegno continuo e modelli organizzativi evoluti.
In altre parole, la relazione tra sicurezza, cultura e produttività costituisce un catalizzatore ideale per migliorare ogni area di un’azienda. Questa relazione che non è esagerato definire strategica si può costruire attraverso quella che gli addetti ai lavori chiamano “disciplina ergonomica”.
Di cosa si tratta? L’ergonomia studia e ottimizza le stazioni di lavoro calcolando il tempo e la fatica necessari per ogni movimento compiuto dal singolo operaio. L’obiettivo è eliminare la fatica dalla fabbrica ottenendo un aumento della produttività ed una contestuale riduzione del rischio ergonomico.
Accanto alla valorizzazione dell’ergonomia si è posta, negli ultimi anni, l’innovazione tecnologica, offrendo grandi prospettive di sviluppo anche in ottica di health and safety 4.0. Molte aziende stanno testando le più recenti tecnologie ergonomiche anche in contesti industriali.
Robotica collaborativa, esoscheletri, realtà aumentata sono tecnologie legate all’implementazione di Industria 4.0 che necessitano di standardizzazione e per le quali gli indispensabili requisiti tecnici di sicurezza non possono prescindere dalle peculiarità fisiche, sensoriali e psicologiche dell’uomo e da aspetti quali l’usabilità e l’accettabilità di tali tecnologie nello svolgimento del proprio lavoro.
Un gruppo di lavoro che si occupi degli aspetti di ergonomia nell’Industria 4.0 e nella fabbrica intelligente: la Call for experts è stata avviata nel mese di maggio 2017 dalla Commissione Tecnica dell’ISO TC159, presieduta dalla tedesca DIN.
La robotica collaborativa
I robot collaborativi, o cobot, sono robot industriali di nuova generazione pensati per affiancare gli operatori e interagire con loro senza barriere o gabbie protettive a dividerli.
Il termine “cobot” è stato introdotto per la prima volta nel 1996 da due professori della Northwestern University progettando un manipolatore intelligente (Intelligent Assistant Device) per General Motors. Oggi il termine, anche in ambito normativo ISO, viene utilizzato per identificare una tipologia di applicazioni che hanno come comune denominatore una condivisione dello spazio di lavoro tra operatore e robot in assenza di barriere fisiche.
L’obiettivo della collaborazione è quello di enfatizzare e integrare le capacità proprie dell’uomo di percezione, flessibilità, abilità, ed esperienza con la forza, la resistenza, la precisione e la ripetibilità del robot.
L’industria è stata uno dei primi settori nel quale sono stati introdotti robot per sostituire l’uomo in compiti usuranti e/o pericolosi, con una netta divisione dello spazio operativo a garanzia della sicurezza degli operatori. Oggi tali barriere di separazione si stanno tramutando in protezioni software di tipo più evoluto per consentire la condivisione dello stesso spazio operativo. I cobot oggi in commercio, grazie a telecamere e speciali sistemi di anticollisione, assicurano il blocco del robot al primo contatto con le persone, evitando la possibilità di incidenti, ma precludono di fatto una reale possibilità di interazione con l’operatore umano. La collaborazione fisica tra persone è garantita dalla capacità degli esseri umani di percepire spazi, dimensioni e forze in gioco, elementi oggi assenti nei robot.
La necessità di un’ulteriore evoluzione della robotica
Si pensi però, ad esempio, al progetto europeo Andy (Advancing Anticipatory Behaviors in Dyadic Human-Robot Collaboration), coordinato dall’Istituto Italiano di Tecnologia, che si pone tra gli obiettivi di ricerca lo sviluppo di dispositivi indossabili in grado di misurare i movimenti e gli sforzi compiuti dagli operatori e di comunicarli alle macchine, così che imparino a prevedere e interpretare il comportamento umano. In particolare, i ricercatori del laboratorio HRI2 (Human Robot Interaction) dell’IIT, che si occupano della collaborazione uomo-macchina in contesti industriali si sono posti un obiettivo ambizioso per il prossimo futuro “i robot dovrebbero essere in grado di riconoscere eventuali condizioni di lavoro improprie e quindi adattare il proprio comportamento per migliorarle”. Tali metodi dovrebbero prevenire stress e infortuni legati al lavoro e mantenere una buona salute e produttività degli operatori umani. Per raggiungere questo obiettivo, è necessario migliorare e combinare diversi elementi cruciali negli attuali campi della robotica. Il robot deve, infatti, conoscere lo stato del corpo umano, i limiti del controllo motorio umano, la risposta umana a compiti impegnativi, monitorare il movimento e altri stati dell’umano per sapere quando e come assistere, oltre a possedere un quadro di controllo appropriato e capacità di apprendimento per essere in grado di controllare e adattare il proprio comportamento al fine di aiutare il collaboratore umano nel raggiungimento di condizioni di lavoro più ergonomiche.
Le novità normative
Emerge quindi che la sfida tecnologica è tutta aperta per riuscire a facilitare le condizioni di lavoro ergonomiche dell’uomo, molti sono anche gli elementi di discussione in termini normativi. Dal 2016 è in atto la normativa sulla sicurezza ISO10218/TS 15066, nata per rispondere alle nuove esigenze emerse dal diffondersi dei cobot, che fornisce delle specifiche da rispettare per la prevenzione e il controllo dei rischi nell’utilizzo di robot collaborativi. Come evidenziato da molti studiosi, uno dei principali deterrenti ai sistemi integrati uomo-robot è l’attuale punto di vista predominante robot-centrico nella progettazione. La stessa specifica tecnica ISO/TS 15066: 2016 precisa gli aspetti tecnici da tenere in considerazione durante la progettazione di una soluzione collaborativa, evidenziando le caratteristiche dei sistemi di comando da utilizzare nelle celle robotizzate. Manca tuttavia un corpo normativo adeguato che consenta ai robot di collaborare fattivamente con l’uomo, determinando benefici concreti, in termini di benessere psico-fisico del lavoratore e di produttività.
Robot sempre più leggeri e morbidi
Nel progetto meccanico di un robot, l’eliminazione di spigoli vivi e la sostituzione dei bracci in acciaio con strutture più leggere, possibilmente deformabili, con protezioni passive sull’intera struttura, possono ridurre le conseguenze di impatti inattesi durante il funzionamento. Sistemi di sensori e architetture di controllo devono consentire al robot di comprendere e assecondare movimenti ed intenzioni delle persone presenti nell’ambiente di lavoro. Forme non ostili, basse velocità, traiettorie regolari e morbide, manovre prevedibili sono aspetti altrettanto importanti per rendere la presenza del robot “cognitivamente accettabile”. A oggi i robot collaborativi sono caratterizzati da capacità di carico limitate, lentezza nei movimenti e costi piuttosto elevati. Incrementare il pay-load oltre la decina di kg, rendere possibile l’effettiva mobilità dei robot su piattaforme mobili capaci di navigare all’interno dei siti produttivi e di posizionarsi in modo accurato per consentire l’esecuzione finale del task sono punti cruciali per la loro diffusione e che devono realizzarsi assicurando sicurezza e benessere psico-fisico dell’operatore.
Gli Esoscheletri Industriali
Un particolare tipo di cobot sono gli esoscheletri attivi, per i quali le considerazioni di sicurezza e benessere psico-fisico dell’utilizzatore sono aspetti di massima rilevanza e di grande complessità tecnica e normativa. Realtà già oggi presenti nel campo della riabilitazione, l’introduzione di esoscheletri attivi nel contesto industriale è al momento preclusa (almeno in Italia) dalla mancanza di normative.
Gli esoscheletri sono dispositivi indossabili, strutture meccaniche esterne che supportano il corpo e/o ne aumentano forza e resistenza (se attivi). Sviluppati in ambito militare e riabilitativo, gli esoscheletri per applicazioni industriali sono oggi una realtà in forte sviluppo. Da Ford, ad esempio, che ha sperimentato l’utilizzo di esoscheletri industriali, fanno sapere, che “grazie alla progressiva introduzione di tecnologie a supporto del miglioramento ergonomico” nei propri impianti, si è ottenuto “una diminuzione del 90% delle problematiche legate all’ergonomia, dovute a movimenti eccessivi o alle attività su componenti difficili da installare”.
Così sta facendo in Italia anche FCA, che nel 2018 ha lanciato MATE, un esoscheletro passivo indossabile che aiuta a sollevare le braccia e quindi facilita le operazioni che coinvolgono la spalla e quelle, ad esempio, sotto scocca che prevedono delle posture cosiddette incongrue (per intendersi, le mani alzate sopra la testa, come se si dovesse cambiare una lampadina).
I benefici degli isoscheletri
I potenziali benefici offerti dagli esoscheletri riguardano: il limitare possibili situazioni di affaticamento del lavoratore, offrire la possibilità di prolungare la vita lavorativa di personale qualificato oltre a ridurre l’incidenza e l’insorgenza di disturbi muscolo-scheletrici. Gli studi di efficacia al momento si sono concentrati soprattutto sui possibili benefici muscolari, valutando, attraverso elettromiografia di superficie (EMG), i potenziali di attivazione dei principali gruppi muscolari coinvolti durante l’esecuzione di attività di lavoro con o senza esoscheletro. Spesso si tratta di studi di laboratorio su soggetti volontari, utili a valutare l’efficacia biomeccanica del dispositivo, ma che rappresentano soltanto una prima fase nella valutazione dell’applicabilità a un contesto industriale. Occorreranno studi in grado di valutare l’usabilità e l’accettabilità dei lavoratori anche nel lungo termine.
Risulterà poi necessario capire come valutare il carico di lavoro biomeccanico durante attività di lavoro assistite dall’esoscheletro, nonché l’impatto di tali strutture sul lavoro fisico. L’introduzione di questi dispositivi potrà avere ripercussioni importanti nella valutazione del rischio in fase di progettazione e di industrializzazione, con una crescente necessità di utilizzare metodi olistici di valutazione del rischio da sovraccarico biomeccanico che consentano di definire l’effetto di tali sostegni passivi sul carico posturale e sull’uso di forza. Anche sotto questo punto di vista c’è un forte ritardo degli organi normativi, oggi non ci sono strumenti che consentano di valutare il carico biomeccanico in presenza esoscheletri su fattori di rischio come forza e postura. In Francia, si sta elaborando uno standard specifico sulla fase di test di applicazione di esoscheletri industriali, ma la cui uscita è prevista per il 2021. Una delle sfide dell’industria del futuro sarà quindi quella di capire come gestire la forza lavoro in modo più efficiente, valorizzando l’ergonomia e attuando cambiamenti dei modelli organizzativi verso forme evolute e strutturate. Quello che oggi è chiaro è che i fattori umani e l’ergonomia giocheranno sempre più un ruolo importante nella trasformazione e rivoluzione tecnologica che sta vivendo la fabbrica.